HERMA: Linerless side labeling at Rapunzel
News General news
- At organic food manufacturer Rapunzel, a HERMA InNo-Liner system applies the label that is crucial in the logistics chain to the outer packaging.
- The linerless system found its way into production via the flagship company's sustainability concept.
- Says Rapunzel, "With the elimination of the liner, the HERMA InNo-Liner system is right on our sustainability line."
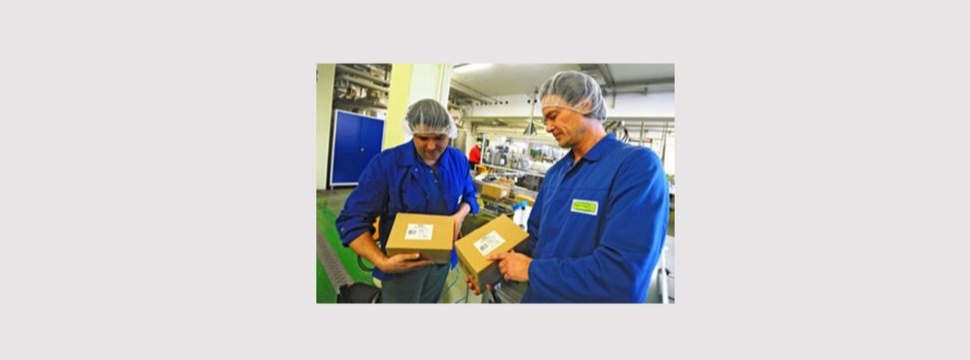
Around half of all products from the Rapunzel premium organic brand are produced or packaged at the company's headquarters in Legau in the Allgäu region of Germany. In the fastest packaging line, a HERMA InNo-Liner labeling system is in operation, whose innovative feature and unique selling point is that it does away entirely with the siliconized backing material that is otherwise customary. "2,000 to 3,000 applications come together here per shift in the chickpea repackaging alone, and that quickly gives you an idea of how high the savings potential is," explains Alexander Karst, Production Department Manager. "It is already around 355 kg per year in this one test plant. We've been disposing of that most carefully so far; but if it can be done completely without, it's clear which way is better." The HERMA InNo-Liner labeling system is the first practical solution of its kind in the world to meet the high cycle rates and requirements of modern packaging, shipping and logistics applications, where direct printing of changing grades of cardboard material is out of the question because the print image would then be inadequate. After all, all codes in the downstream logistics chain must always be securely and instantly legible.
Full "sustainability yield" thanks to process reliability
The system is based on a special adhesive design and a specially developed micro-atomization unit that ensures precise, purely water-based adhesive activation only at the moment of dispensing. As a result, the label material, which is not adhesive until then, is wound onto a roll as normal. Another system-related plus, according to Karst, is that "only the label that is actually dispensed is variably printed. Mix-ups or incorrect use of labels that have already been printed are ruled out, both at startup and during line interruptions, since no label hangs in the loop in advance or in progress - a huge advantage for product safety." Admittedly, due to the lack of liner, many more labels fit on a roll. In addition to complete disposal, this also saves handling, storage and transport costs. "And in terms of application, the solution with InNo-Liner is also more economical than a normal adhesive label," says Karst. "In operation and function, however, what is decisive is the efficient labeling process, the clean print image and the reliable adhesion." This is because the outer packaging label controls the entire path of the carton. "And the HERMA label adheres very well." According to HERMA, achieving this adhesion effect within fractions of a second absolutely requires the multilayer technology in the pressure-sensitive adhesive that the self-adhesive specialist is consistently pushing forward. In addition, the HERMA solution ensures that the material, printing and processing are permanently convincing, even at the normally required cycle rate of around 20 labels in A5 or A6 size per minute. After all, the "sustainability yield" of the system can only be fully reaped with absolute function and process reliability. And so, for Rapunzel, the fact that HERMA found its way into production via the flagship company's sustainability concept is unreservedly worthwhile: "With the elimination of the carrier tape, the HERMA InNo-Liner system is right up our alley."