How Laakirchen Papier AG optimizes the papermaking process with OnEfficiency.Strength
News General news
Current raw material prices are forcing paper manufacturers to reduce production costs and further optimize the efficiency of their production facilities. Digitalization plays a key role in achieving efficiency gains and cutting costs. This is because new technologies in particular enable significant improvements in existing and new plants. They allow better monitoring of all processes and thus more precise production control, which in turn leads to higher efficiency and better availability.
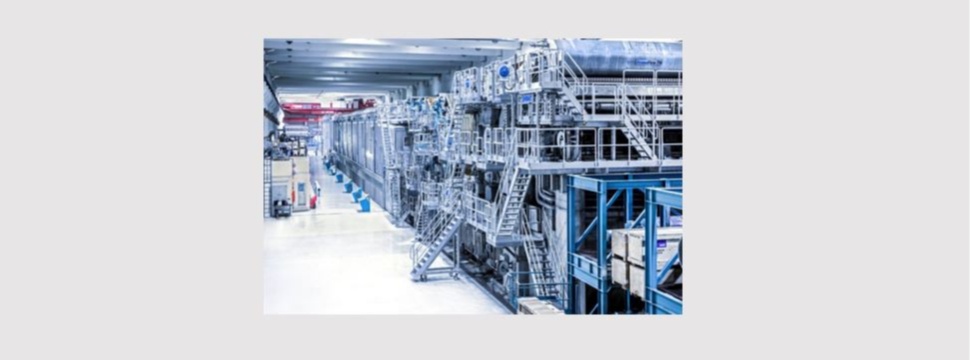
Reduced starch consumption
In addition to fiber, starch is a major raw material cost factor in the production of packaging papers. Therefore, the goal of paper manufacturers is to reduce starch application and keep the amount of starch as low as possible – without falling below the required quality level. However, continuous optimization with conventional tools quickly reaches its limits. Paper manufacturers are confronted with the situation that they cannot directly control important quality parameters such as strength, because the measurement of the relevant parameters only takes place at the end of each tambour in the laboratory and the values are not continuously available.
Digital solutions such as OnEfficiency.Strength from Voith now offer the ability to have important quality parameters constantly available thanks to virtual sensors and to have the process optimally controlled automatically.
How Laakirchen Papier AG optimizes the use of starch
Since 2021, OnEfficiency.Strength has been used at PM 10 in Laakirchen, Austria, to optimize starch application. A positive side effect is also the resulting reduction in steam consumption in the after-dryer section.
What was previously only possible either through manual measurements in the laboratory or automatic test line measurements is now realized by Laakirchen with the use of virtual sensors: the calculation of data on the most important strength values (SCT CD, CMT and burst).
Real-time prediction of quality parameters and continuous optimization of the process has not only prevented quality fluctuations, but OnEfficiency.Strength has also enabled production costs to be reduced while reliably meeting quality targets.
For PM 10, OnEfficiency.Strength helped to save four percent starch in the first year and now up to 10 percent starch in the second year, while key quality parameters such as SCT CD and CMT remained within target values.
The OnEfficiency.Strength principle: visualize, stabilize, optimize
OnEfficiency.Strength combines three modules to create a new, powerful generation of advanced process controls (APC). The control system includes virtual sensors, also called soft sensors; model predictive control (MPC); and a cost optimizer. A special feature of the virtual and self-adaptive sensors is their high predictive accuracy, typically above 90 percent.
The virtual sensors precisely predict important quality parameters. Knowing these parameters in real time enables the MPC to control the papermaking process in such a way that the targeted values are permanently achieved through continuous adjustment. The cost optimizer ensures that this is done at the lowest possible cost. To find the customer-specific cost optimum, actuators and control strategies can be individually selected and flexibly adapted.
Laakirchen Papier AG was particularly impressed with the high savings potential offered by OnEfficiency.Strength. This was calculated in the Value-Add Assessment carried out in advance.