ProJet receives order for two high pressure cleaners from Siam Kraft, PM1, Thailand
News General news
ProJet received an order for the supply of 2 new high pressure showers, which will be delivered to PM1of Siam Cement Group (SCG). SCG is the holding company of Siam Kraft, Thai Kraft, Thai Cane, all located in Thailand and Vinakraft, located in Vietnam.
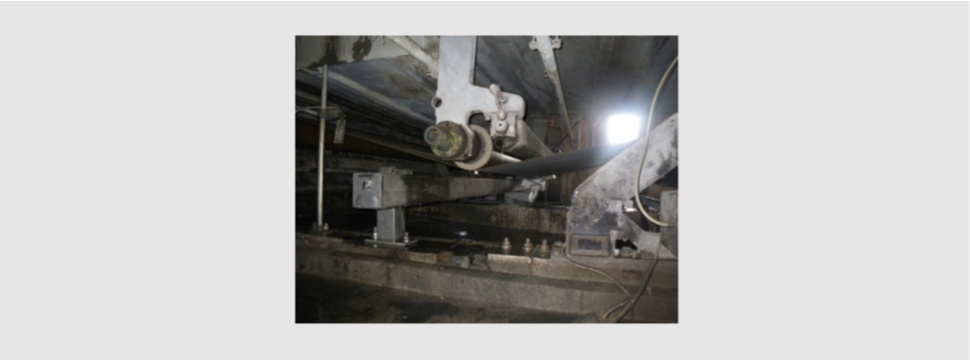
ProJet will supply 2mhigh pressure showers for Press Felts for PM1 located in Thailand. PM1 produces kraftliner and/or corrugated medium at a width of 5000mm (200 in.) and an average speed of 800m/min (2400fpm). Most of SCG’s machines were already equipped with some ProJet showers, now PM1’s felts will be equipped with these as well.
The ProCleaner Type F (Forming Fabrics) and Type P (Press Felts) use a single traversing head that cover the felts almost three times as fast as the existing conventional oscillating showers. Furthermore, SCG expects to achieve substantial water savings becasue the ProJet Cleaner uses only 1.3gpm (5.0litre/min) of water; a conventional shower consumes over 40gpm.
The order was received in June 2022 and delivery of the Cleaners is expected in December 2022.
The ProCleaner use a single traversing head that cover the fabrics almost three times as fast as the existing conventional oscillating showers. Furthermore, SCG expects to achieve substantial water savings because the ProJet Cleaner uses only 5.0litre/min of water; a conventional shower consumes over 160 l/min.
Furthermore, the Pro Cleaner delivers the following operational and performance benefits:
- Substantial cleaning water savings (= operational cost reduction + improved profitability): the Pro Cleaner provides superior cleaning performance, while only consuming 1.3gpm (5.0 liter/min) of water. A conventional oscillating shower consumes over 100gpm of water, leading to substantial more electrical power and waste water treatment costs.
- Water mist elimination is achieved by the application of air knives that contain water mist and contamination, which is discharged through Venturi tubes and finally into a save all pan.
- Targeted cleaning enables an operator to control the Cleaner for not only overall CD fabric/felt cleaning but to also apply targeted zone/strip or edge cleaning.