ProJet provides technical service to Fitesa s.r.l., Trezzano Rosa, Italy
News General news
Despite of COVID19 travel restrictions, ProJet continues to fully support customers throughout the world for service and start-ups. On August 18, service was performed on ProJet equipment on the “OMEGA-line” at Fitesa Italy. The Belt Cleaning System was already supplied in 2002, almost 20 years and is still running smoothly. The service performed was part of regular, preventative maintenance and was performed on pump, water heater and the belt cleaner itself. Simone Finardi, Maintenance Manager, stated: “ProJet performed the maintenance quickly and professionally. Now, the equipment is ready again to run another 20 years.”
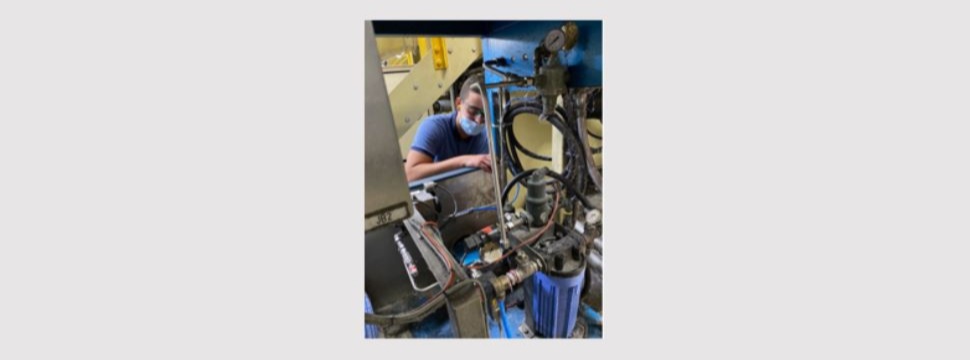
ProJet has a team of 5 young and dynamic service engineers, that travel the world to service ProJet equipment, perform start-ups and measure-up all kinds of continuous manufacturing lines for new ProJet equipment.
Spunmelt nonwoven production: Spunbond & Meltblown
Fitesa s.r.l. has a nonwoven manufacturing process, called spunmelt extrusion. Spunmelt is a combination of Spunbond and Meltblown; in the Spunbond process polymer granules are melted and molten polymer is extruded through spinnerets. The continuous filaments are cooled and deposited on to a conveyor belt to form a uniform web. In Meltblown web formation, low viscosity polymers are extruded into a high velocity airstream on leaving the spinneret.
Contamination on the process belts
Both Spunbond and Meltblown are known to create contamination issues on the conveyor belt (also known as spinbelt), each process having its specific characteristics and belt contamination issues. Belt contamination reduces runnability of the production line and therefore output of nonwoven hygienic material of the whole plant.
The solution
ProJet b.v. delivered a continuous spinbelt cleaning system, the Power Cleaner, which continuously, 24h/day, cleans off effectively all types of contamination. Using a brush to clean of “ropes”, high pressure heated water for monomer, short meltblown fibers, dust and spin finish, the Power Cleaner system will maintain optimum permeability of the belts throughout the life and significantly increasing lifetime of the belt. By doing so, runnability of the machine is optimized and quality of the web is secured.