ProJet successfully starts up Tail Cutter & Deckle Cutter at Strathcona Paper, Napanee, ON, Canada
News General news
ProJet, Meerssen, Netherlands have successfully started up 1 Tail & Deckle Cutter at Starthcon Paper in Canada.
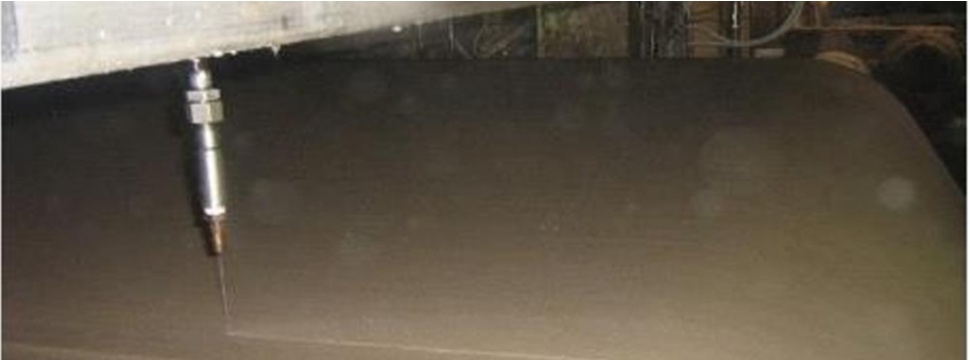
Despite of all COVID regulations and travel restrictions, ProJet fully supported the customer and a joint successful commissioning of the systems was achieved. Strathcona is producing board on a 126 in. wide machine with very frequent deckle changes. Strathcona selected ProJet as preferred supplier because ProJet’s Tail & Deckle Cutter excels in quality, reliability and user-friendliness.
After careful installation of the Tail Cutter, detailed task planning for all teams involved, numerous checks on all safety aspects, ProJet’s expertise helped to complete the commissioning in just a couple of hours. The engineers conducted a number of installations, hardware and I/O checks, after which start-up was just “plug and play”, thanks to the user-friendly ProJet system, according to all teams involved.
ProJet’s Tail & Deckle Cutter has the following features:
- Automated trim removal before the couch and size press
- Eliminates changing deckle widths of suction and press rolls
- Substantial savings in drying energy possible if trim is removed at the wet-end instead of after the reel
This leads to the following benefits:
- Adjusting the paper width to cross directional shrink => Minimum paper loss at pope roller
- Parameter feedback: “End of production run” or “All parameters ready to go for new production run” => Unproductive time between production runs is minimized.
- Setting the Tail width => Quickest possible adjustments.
- Choosing the position of the Tail => Best position of the press rolls or press felts
- Choice for dual speed => Optimal speed for “Go to full width” and thus minimizing the risk for sheet breaks. => Highest possible speed at “Cut off” and thus reducing scrap to a minimum.
- Remote control => Operating personnel does not need to wait at the forming section during tail transfer=> reduction of labor