ProJet nimmt erfolgreich Tail Cutter & Deckle Cutter bei Strathcona Paper, Napanee, ON, Kanada in Betrieb
News Allgemeine News
ProJet, Meerssen, Niederlande hat erfolgreich einen Tail & Deckle Cutter bei Starthcon Paper in Kanada in Betrieb genommen.
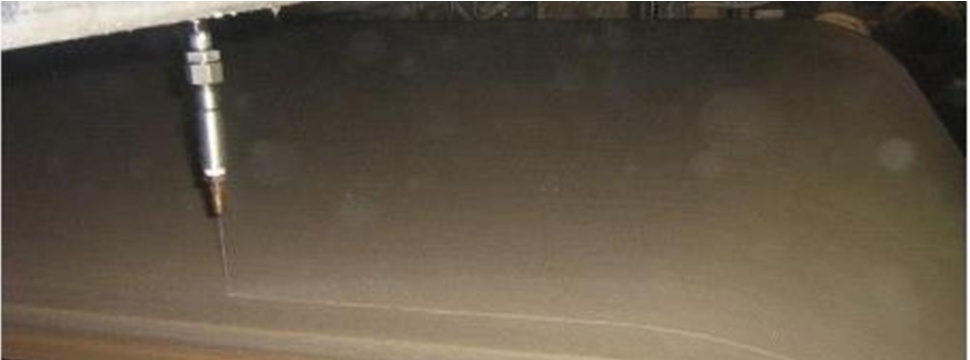
Trotz aller COVID-Vorschriften und Reisebeschränkungen hat ProJet den Kunden voll unterstützt und eine gemeinsame erfolgreiche Inbetriebnahme der Systeme erreicht.
Strathcona produziert Karton auf einer 126 Zoll breiten Maschine mit sehr häufigen Deckle-Wechseln. Strathcona entschied sich für ProJet als bevorzugten Lieferanten, weil der Tail & Deckle Cutter von ProJet sich durch Qualität, Zuverlässigkeit und Benutzerfreundlichkeit auszeichnet.
Nach einer sorgfältigen Installation des Tail Cutter, einer detaillierten Aufgabenplanung für alle beteiligten Teams und zahlreichen Überprüfungen aller Sicherheitsaspekte konnte die Inbetriebnahme dank der Expertise von ProJet in nur wenigen Stunden abgeschlossen werden. Die Ingenieure führten eine Reihe von Installationen, Hardware- und E/A-Prüfungen durch, nach denen die Inbetriebnahme dank des benutzerfreundlichen ProJet-Systems einfach "Plug and Play" war, so die Aussage aller beteiligten Teams.
Der Tail & Deckle Cutter von ProJet hat die folgenden Eigenschaften:
- Automatisches Entfernen des Beschnitts vor der Gautsch- und Leimpresse
- Eliminiert den Wechsel der Deckelbreite von Saug- und Presswalzen
- Erhebliche Einsparungen bei der Trocknungsenergie möglich, wenn der Beschnitt am Nassende statt nach der Aufrollung entfernt wird
Daraus ergeben sich die folgenden Vorteile:
- Anpassung der Papierbreite an den Quereinzug => Minimaler Papierverlust an der Papprolle
- Rückmeldung der Parameter: "Ende des Produktionslaufs" oder "Alle Parameter bereit für neuen Produktionslauf" => Unproduktive Zeit zwischen den Produktionsläufen wird minimiert
- Einstellung der Streifenbreite => Schnellstmögliche Anpassung.
- Wahl der Position des Hecks => Beste Position der Presswalzen oder Pressfilze
- Wahl der doppelten Geschwindigkeit => Optimale Geschwindigkeit für "Auf volle Breite gehen" und damit Minimierung des Risikos von Bogenabrissen. => Höchstmögliche Geschwindigkeit beim "Abschneiden" und damit Minimierung des Ausschusses.
- Fernsteuerung => Das Bedienpersonal muss während der Streifenübergabe nicht an der Formanlage warten=> Arbeitsersparnis