RRK Wellpappenfabrik invests again in quality and further growth
News General news
The year 2021 marked for RRK Wellpappenfabrik GmbH & Co. KG in Bottrop not only marked the 45th anniversary of its founding. Investments were also made in the anniversary year, and in September of this year another, new rotary die cutter for the highest-quality packaging in flexographic printing (HQPP) was put into operation. The new press impresses with its working width of 2,800 mm, high production speed, fully automated peripherals and a wide range of quality-determining additional equipment.
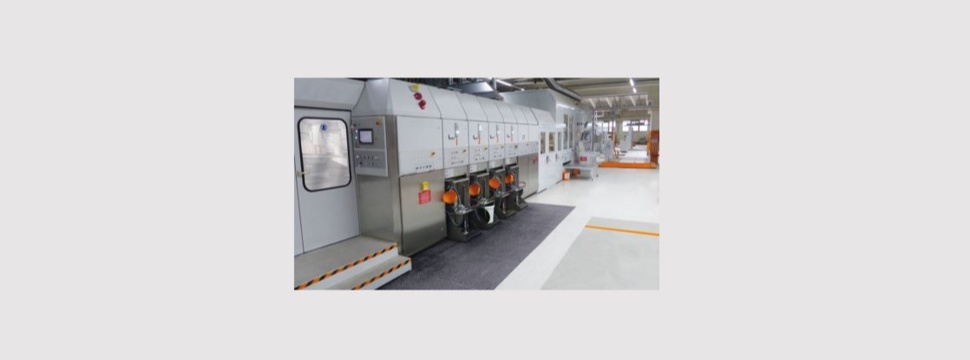
Over the past five years, the company, which was founded in 1976, has experienced growth in every respect. The continuous investments in state-of-the-art plant and building technology as well as logistics, which have amounted to more than 20 million euros since 2016, have certainly played their part in this.
The recently commissioned rotary die cutter has, among other things, four inking units with drying, print image monitoring including ejection and packing robots. Complete camera monitoring of the entire system, optimized sound insulation measures and consistent design under lean management and 5S methods create new, state-of-the-art workplaces for the Panther team on the line. The decision in favor of the machine was made against the background of increasing customer demands for quality in a wide variety of corrugated packaging: Thanks to state-of-the-art process technology and quality monitoring, higher production speeds and the streamlined workflow, the RRK Wellpappenfabrik is thus increasing its capacities and also providing itself with more flexibility with a view to customer requirements. Extensive work has been implemented at the Panther plant in Bottrop since the spring to make optimum use of the machine's features. In order to optimize the long design of the machine, the infeed and outfeed were partly moved and positioned next to the line in a space-optimized manner. Internal adjustments to the building conditions, including a creative solution for transporting the diecutting waste and an extension for storing clichés and diecutting tools, complete the overall concept.
Since the beginning of September, the new converting machine has been producing printed and die-cut packaging, which will be followed by many millions of square meters of sophisticated finished corrugated board in the coming years with the expanded capacities.