Valmet and CMPC sign letter of intent for the modernization of Guaíba pulp mill in Brazil
News General news
Valmet and CMPC have signed a letter of intent (LOI) for Valmet to deliver key technology for the BioCMPC project. The target of the project is to increase the production capacity of the Guaíba pulp mill’s line 2 from 1.5 million ADt/y (air dry tonnes per year) to 1.85 million ADt/y. The modernization is expected to start operation in the fourth quarter of 2023.
Valmet and CMPC target to finalize the contract during October 2021.
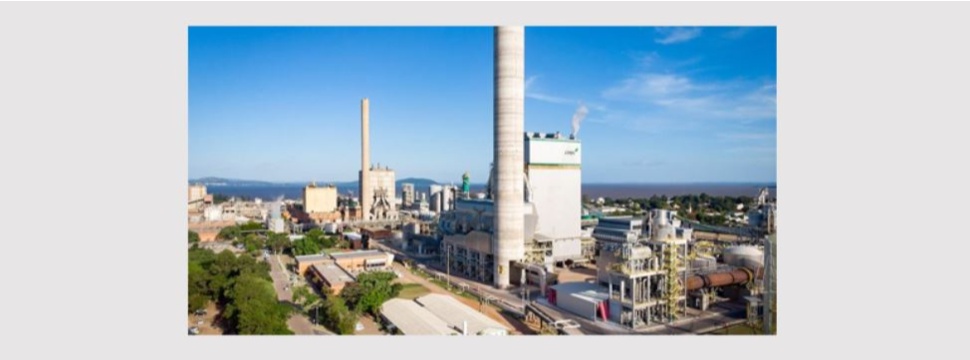
This expansion project, BioCMPC, targets both to increase the production capacity of the Guaíba mill and also improve the environmental performance with for example increased production of renewable electricity and minimized water usage in pulp production process.
“Valmet delivered the CMPC’s Guaíba mill line 2 in 2015 and the mill has been a showcase for many of our technologies. Over these years we have introduced value adding industrial internet solutions and offering our expert services for mill maintenance. To be chosen as the main partner for this remarkable project reinforces Valmet’s commitment for a more sustainable future,” says Celso Tacla, Area President, South America, Valmet.
“With this project we will continue delivering the best technology available combined with leading automation and industrial internet solutions for efficient and even more sustainable pulp production. This delivery will feature our latest technology to lower water usage, reduce emissions and eliminate odorous gases. Our experts will support optimizing the mill performance both onsite and remotely,” says Bertel Karlstedt, Business Line President, Pulp & Energy, Valmet.
Technical information about the delivery
Valmet’s delivery for the Guaíba pulp mill line 2 modernization will include rebuild of the pulp drying, fiberline, evaporation and white liquor plant, a new recovery boiler and new ash treatment, extended distributed control system including advanced industrial internet features. The technology delivery is supported by spare parts packages. The upgraded line is optimized for high reliability and performance with low environmental impact.
The pulp drying line upgrade will increase the drying and baling capacity and performance with the same high operational safety requirements that always guide Valmet’s projects. The upgrade includes improvements to screening and drying, automatic tail threading and an additional baling line.
The fiberline upgrade includes cooking plant technology update, fiberline improvements in brown stock and post oxygen washing and a new additional bleaching stage. The upgrade gives flexibility to minimize water usage and effluent generation improving the fiberline sustainability and environmental KPIs.
The white liquor plant upgrade includes capacity increase of the recaustisizing and lime kiln. The modernized lime kiln electrostatic precipitator (ESP) and lime mud disc filter will ensure low emissions.
The evaporation plant will be upgraded to process 2,000 t water per hour. The eight-effect design provides high steam economy and features robust and reliable Valmet Tubel design. Improved condensate treatment will lower water consumption of the mill.
The new recovery boiler will have a design capacity of 1,900 tds/d (tonnes dry solids per day) and will feature several high-power features for low energy consumption and high steam generation. The delivery also includes electrostatic precipitators (ESP) tailored for recovery boiler conditions. The recovery boiler ash will be treated with Ash Leaching Duo technology offering easy operation and improved leaching efficiency to maximize cooking chemicals recovery.
The CMPC Guaíba mill has already been the benchmark of the industry as an odorless mill. The collection and handling of the mill’s odorous gases is further improved with NCG upgrades across process islands.
The automation delivery includes Valmet DNA distribute control system, advanced process controls (APC) for selected process areas, analyzers and online measurements.
The delivery is supported with extensive Valmet Industrial Internet (VII) services package with onsite and remote expert support. The VII services include Valmet Performance Center support, Data Discovery, Dynamic Center Line Advisor, Performance Monitoring tools and Operator Training Simulator.