
News for the pulp and paper industry
Do you want to learn more? Here you will find news about paper and the paper industry, they are also sorted by different categories - General news from the paper industry, jobs, trade fairs, offers and requests. Would you also like to appear with your press releases here? Just contact us.
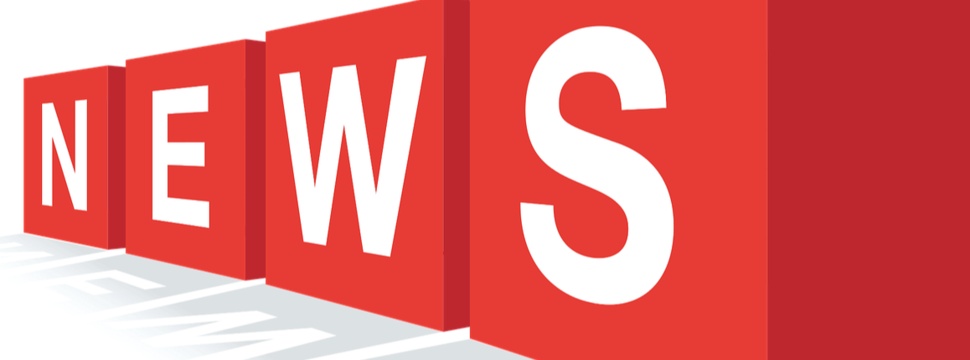
This page shows you the latest news from all paper-world.com news categories (General news from the paper industry, jobs, trade fairs, offers and requests).
You want to see general news regarding the pulp and paper industry?
Find the appropriate category and read the interesting news. Here companies are looking for employees or employees are searching for a new job, companies report about innovations or their new sales manager. Other companies inform about their participation in trade fairs or about surpluses from production that can be sold at favorable prices.
Are you looking for a new employee? You have developed a new and innovative paper packaging? You participate in a trade fair and exhibit your new products there? You urgently need filter paper and are looking for a distributor who has it directly in stock?
If you answered "yes" to at least one of these questions, then you have come to the right place.
Would you also like to publish your news here? Get in touch with us. Just use our contact form.
Birkner hopes you enjoy reading these news.