Balancing act for Stora Enso as paper market rebounds
News General news
Recent raw material scarcity and cost inflation in the paper business have led to higher price hikes, while industry restructuring combined with economic recovery have caused overbooking. But the market outlook is more balanced, with Stora Enso having competitive and sustainable paper assets for the benefit of its customers.
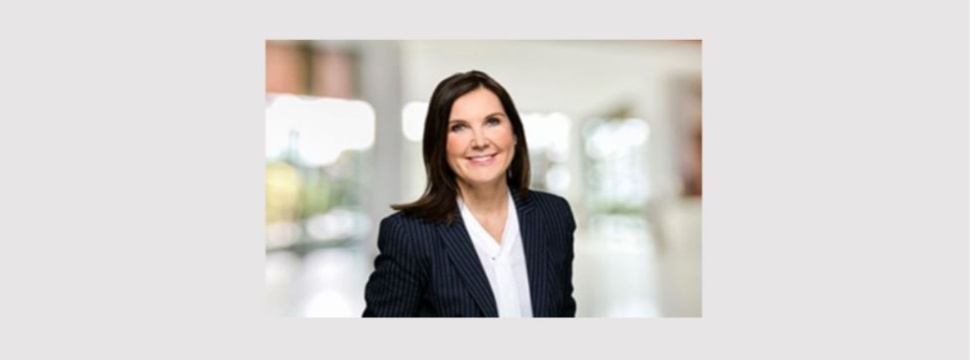
“While the pandemic put a tail wind into some businesses, including packaging and wooden building solutions at Stora Enso, it really put a headwind into ours,” laments Kati ter Horst, EVP, Stora Enso, Paper division.
With 25 years in the business, ter Horst has never seen anything like the paper industry of the last year and half. Demand for paper has been inching down annually in Europe since 2007, but nothing close to the historical 18 percent fall seen during 2020. Paper prices also plummeted, reaching an all-time low in the summer of 2021.
“This is why current unavoidable price hikes in the face of rising raw material and energy costs, may seem steeper than they actually are,” ter Horst explains, “because they’re coming from such a low benchmark.”
Scarcity of raw materials
The stay-at-home lifestyle during lockdown that sparked an unprecedented rise in e-commerce also exploded the market for brown box making, which uses partly the same recycled fibre raw material as paper producers. “This has made it difficult to source and inflated the price,” says ter Horst.
On the other side, a marked drop in the production of virgin paper during the pandemic meant a corresponding lack of paper going back into the industry’s circular economy. This combined with restructuring and economic recovery means Stora Enso’s Paper division now finds itself overbooked with more orders than they can fill.
“It’s been challenging for our customers and challenging for us too,” says ter Horst, who is urging customers to be patient. “But price increases will need to continue for a while as we work to bring everything back into balance.”
Closing out capacity
Stora Enso has certainly done its share in taking out overcapacity from the industry. Ter Horst cites two painful and high-profile mill closures at Veitsiluoto in Finland and Kvarnsveden in Sweden, as well as a successful mill conversion in Oulu and some successful divestments of other mills
“This has stripped us down to only our most competitive assets,” ter Horst says, “so as things normalise, we’ll be even better positioned to serve our customers.”
Good green news
There has also been good news for customers in sustainability. Most recently with the announcement of a new biogas partnership with Gasum at the Nymölla Mill in Sweden. The new joint onsite plant is turning residue water into green energy to produce biogas for long-haul transportation fleets. Paper division has also invested in targeted CO2 reductions and bioenergy, in Maxau and most recently in Anjala and Nymölla mills.
Stora Enso’s paper mills already consume a minimum amount of water, with 96 per cent of process water being purified and returned to source. The mills also target zero waste with almost nothing going to landfill. “By reducing all these environmental impacts,” ter Horst asserts, “we’ve also been contributing to our customers’ sustainability performance.”
Digital services score high
During the pandemic, digital services also became core to her division’s customer service offering, characterised by an increased uptake of a digital tool called eFlowOnline.
“Using the tool, customers can track their orders and be in touch with us 24/7,” says ter Horst, who is encouraging more customers to sign up. Net promoter scores and customer feedback have shown the tool to be a valued digital customer service platform in the industry. “And that is saying a lot,” ter Horst enthuses.
Customers have also been taking advantage of a growing body of digital solutions designed to help them solve problems from a distance. “Our technical customer service has been particularly well received,” ter Horst recalls “when we haven’t been able to meet in person.”
Opening up again
Now with things opening up, she is keen to get out from behind her computer and visit as many production sites and customers as she can.
They say social distancing comes naturally to Finns, but ter Horst is not your typical Finn. With a strong background in sales, she is a self-described fan of face-to-face to meetings.
“Customers know me, and I’ve really missed getting out and connecting with them in person,” she says.
Ter Horst is also planning to put on her hard hat and gumboots for some mill visits. Stora Enso’s mills all continued operations during the pandemic, and she wants to congratulate the staff. “Our mill workers couldn’t just opt to work from home,” ter Horst recalls. “They had to show up, and a lot was asked of them in terms of finding new ways to do even the simplest things.”
But, wherever ter Horst heads, for now, it will still be into the wind.
“At least until the turn of the year when we will be better positioned to serve our customers, and in a better market.”